Ricardo’s point of view on energy storage and hydrogen development for commercial vehicles
We had a chat with Josh Dalby, Chief Engineer Technology Strategy, and Chief Engineer Trevor Downes about the requirements of light- to heavy-duty commercial vehicles, also mentioning some of the latest project carried out by the global engineering company.
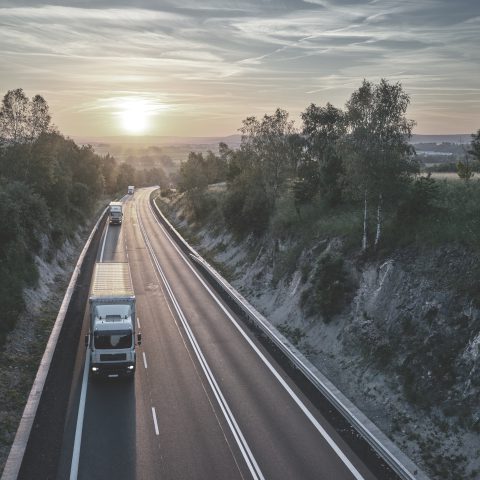
Energy storage and hydrogen development are key issue in the truck and van sector. Ricardo is working on such technologies. That’s why we had a chat with Josh Dalby, Chief Engineer Technology Strategy, and Chief Engineer Trevor Downes about the requirements of light- to heavy-duty commercial vehicles, also mentioning some of the latest project carried out by the global engineering company. It’s the second stage of our inquiry, after the very first interview dealing with the matter of electrification in the truck market.
Energy storage solutions across the truck and van market
Mr Dalby, how’s Ricardo working as for energy storage in light- and medium-duty trucks?
«Ricardo is developing energy storage solutions for applications across the truck and van market. It is likely that truck and van solutions will differ in terms of the approach and the technology to meet the different sets of requirements.
Van battery packs are more likely to resemble passenger car solutions. Most vans are produced by OEMs who also produce passenger cars, hence the development cost is significantly reduced by sharing common modules or packs with suitable passenger car applications. Vans typically have a flat floor and, providing the loading height remains within an acceptable range, a flat pack construction underneath the floor is the most appropriate arrangement, which is the typical arrangement in most passenger cars also.
Although they are not so vocal about it, it can be seen from published materials that most of the heavy-duty OEMs are investigating hydrogen engines
Trevor Downes, Chief Engineer at Ricardo
Many vans have duty cycles (range, charging time) that can be achieved with such an approach. Hence, most van batteries are likely in the near-term to be 400V, with an 80 kWh-120 kWh capacity to enable a 250km – 400km range. For higher range required, the use of a fuel cell (45-60kW) as a range extender will be the preferred solution».
What about trucks, then?
«Medium-duty truck batteries are more likely to resemble heavy-duty packs as the production volumes and market dynamics mean that most OEMs will look to develop a modular pack that can be configured to provide the different energy storage requirements across the range of vehicles in the medium and heavy-duty sector.
Ricardo is developing such a battery concept that can also be configured to handle differing system voltages, which enables development cost sharing across full BEV (600-800V) and future Catenary BEV (1200V-1400V) solutions, building on the 1400V battery concept developed within the PowerDrive project».
Ricardo’s ICoBat technology
Could you please explain more about the ICoBat technology?
«Ricardo’s ICoBat technology is also relevant to this sector. ICoBat is an immersion cooled battery module (using dielectric fluid) that enables significantly faster charging than conventional solutions and with reduced mass. For both the van and truck sector, these benefits are highly attractive as they lead to improvements in range, extender lifetime vehicle utilization time and total cost of ownership, thanks to better cell cooling performance than conventional cold plate solution
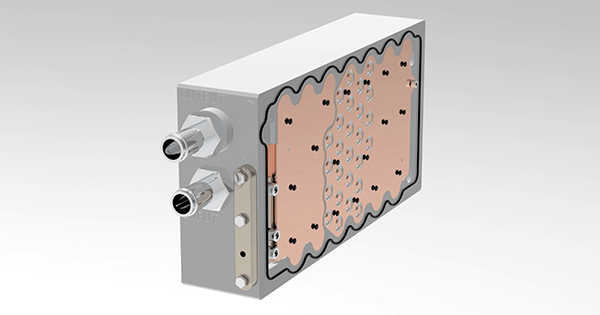
In addition, Ricardo’s Connected Battery Management System platform enables truck and van OEMs and fleet operators to monitor the battery health in the field and identify calibration or vehicle usage updates that can prolong the life of the battery – again delivering an improved total cost of ownership».
The hydrogen engine project carried out by Ricardo
With Chief Engineer Trevor Downes, we closely faced the issue of hydrogen, and the role of Ricardo in the development of such technology for light commercial vehicles.
Mr Downes, could you please say something more about the hydrogen engine project Ricardo is working on?
«Although they are not so vocal about it, it can be seen from published materials that most of the heavy-duty OEMs are investigating hydrogen engines. In the heaviest applications, and if hybridized, hydrogen engines will likely be only slightly less efficient than fuel cells (around 5 percentage points difference at peak power; >5 points difference at lower loads). However, they will be substantially cheaper, come with the benefit of highly reduced reliance on precious metal supply and almost certainly with the robustness and reliability of current diesel engines. Some development will be required to achieve this. A hydrogen engine powertrain will meet the EU definition of a Zero Emissions Vehicle from a carbon point of view. From an air quality perspective, they are expected to easily meet the legislation we see ahead of us now».
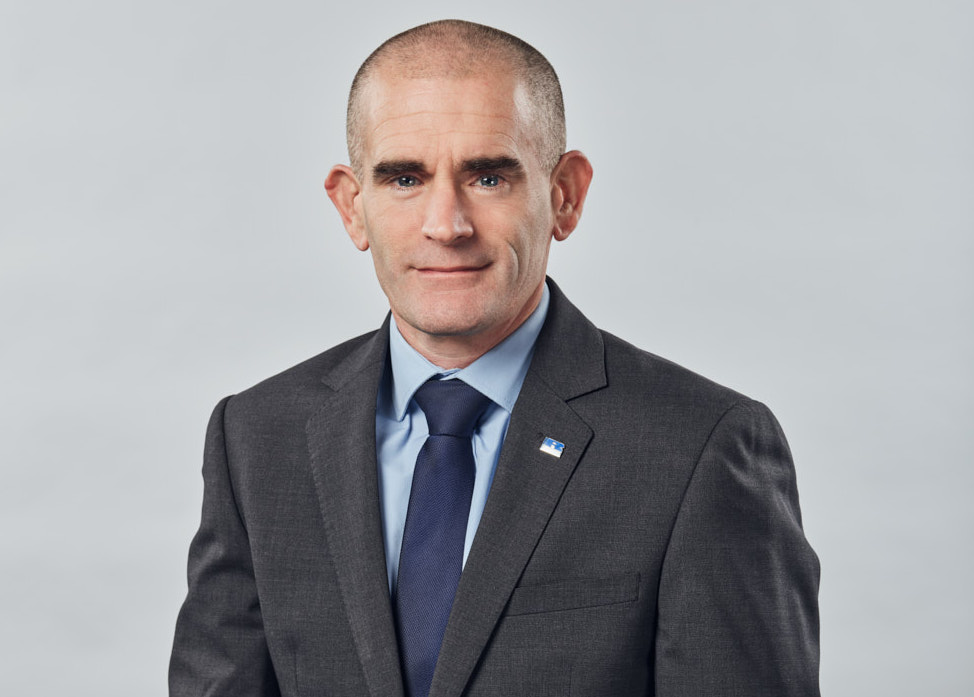
What is Ricardo’s advantage at this stage?
Ricardo has huge experience engineering engines of all types. From our investments into the specifics of engines running on hydrogen, we are leveraging and sustaining the services we currently provide, whilst also helping to investigate – and possibly solve – the challenge of decarbonizing heavy-duty vehicles and equipment in an economically attractive way. By that I mean in terms of both the environmental result, the total cost of ownership of the product and the maintenance of existing supply chains, currently heavily investment in production equipment and trained jobs.
How does your company operate when starting a project?
Our key first step is to understand hydrogen combustion and be able to simulate it in the digital tools that we typically use to carry out specification and concept studies. The hydrogen engine project that we have announced [Ricardo developing and testing new hydrogen engine | Ricardo PLC] runs a Ricardo designed and developed single cylinder research engine to collect detailed combustion and performance data that will then be used to validate our simulations.
Truck and van solutions will differ in terms of the approach and the technology to meet the different sets of requirements
Josh Dalby, Chief Engineer Technology Strategy at Ricardo
This allows us to achieve very high accuracy predictions from our computer models, that helps define the first generation of production hydrogen engines. In addition to this, we are currently installing hydrogen fuel infrastructure in our test facilities in the UK, enabling us to test both hydrogen engines and fuel cells with outputs up to 450 kW. To commission and exercise this facility we are converting a 13-litre heavy-duty natural gas engine to run on directly injected hydrogen. Once the facility commissioning is complete, that engine will be available as a platform for further knowledge generation and development and as an asset that we can provide to customers to enable them to test their own technologies on it, where they don’t have access to one themselves.