ACT Expo, Ballard introduces 9th generation fuel cell engine for zero-emission trucks
The scalable 120 kW fuel cell engine integrates DC/DC regulated output, enabling up to three modules to operate as one system with a single interface, capable of delivering a combined 360 kW of zero-emission power output.
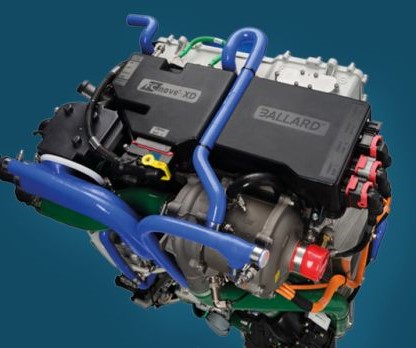
At ACT Expo, Las Vegas, Ballard has recently introduced 9th generation fuel cell engine, the patented FCmove-XD. The latter delivers very high volumetric power density for heavy-duty applications, featuring an engine volumetric power density of 0.36 kW/L and gravimetric power density of 0.48 kW/kg.
Ballard’s revised fuel cell engines: technical details
The scalable 120 kW fuel cell engine integrates DC/DC regulated output, enabling up to three modules to operate as one system with a single interface, capable of delivering a combined 360 kW of zero-emission power output. Furthermore, enabled by an innovative “open architecture” design and other new design advances, the powerful and compact FCmove-XD enables several important performance improvements (as compared to our prior-generation engine), including:
- 120 kW power output from our latest high-performance single stack;
- 33% reduction in total parts count, significantly improving reliability and reducing costs;
- Ultra-high peak system efficiency at >60%, enabling improved fuel consumption (lower total cost of ownership) and efficient heat rejection;
- Wide operating temperature range, up to 95°C;
- Integrated power controller incorporates DC/DC converter, air compressor inverter, and a power distribution unit, along with proprietary software controls, enables improved engine operation and efficiency; and more.
Ballard plans to initially manufacture the FCmove-XD at its Oregon facility, enabling “Buy America” compliance starting in 2025, with future high-volume manufacturing expected at Ballard Rockwall Giga 1, Ballard’s recently announced 3 gigawatt Gigafactory planned to be built in Rockwall, Texas.
“The power and performance requirements of the highly-segmented truck market are particularly demanding due to various use cases, including high vehicle utilization rates and payload requirements,” said Silvano Pozzi, Vice President, Product Line Management. “One of the compelling features of our new FCmove-XD is scalability based on modularity. We can offer customers efficient integration of 120 kW, 240 kW, and 360 kW solutions dependent on truck class, use case, and duty cycle. For example, two engines, totalling 240 kW of power output, can be easily installed in the engine compartment of a typical Class 8 heavy-duty truck, enhancing standardization and redundancy.”