Mitsubishi FUSO trials driverless tow tractor, together with EasyMile
The driverless tow tractor delivered vehicle components in the outside areas of its Kawasaki, Japan plant. The verification took place for a total of six days. Assuming the delivery of vehicle engines, TractEasy covered a distance of approximately 900 meters from the engine manufacturing building to the vehicle assembly lines.
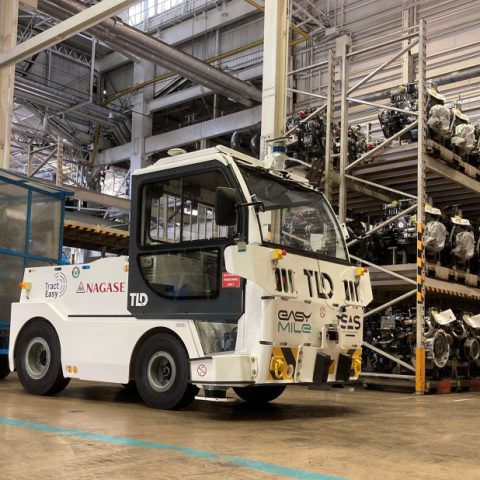
Mitsubishi FUSO trialed autonomous driverless tow tractor, together, relying on EasyMile’s autonomous technology with remote operation in the Mitsubishi FUSO Truck & Bus Corporation (MFTBC) factory environment. The driverless tow tractor delivered vehicle components in the outside areas of its Kawasaki, Japan plant. The verification took place for a total of six days. Assuming the delivery of vehicle engines, TractEasy covered a distance of approximately 900 meters from the engine manufacturing building to the vehicle assembly lines. It successfully maneuvered independently and efficiently on the predetermined route and kept to production schedules.
The driverless tow tractor working in Japan
TractEasy has already been deployed by Daimler Truck, the parent company of MFTBC, at their Wörth, Germany plant. It is the most-deployed autonomous towing solution in the world, also being used by a growing number of other, large vehicle manufacturing plants in North America and Europe, as well as at major international airports including in a fleet at Changi in Singapore, at Narita in Tokyo, with more to come later this year.
MFTBC has been investing in new technologies as part of its “Factory of the Future” project to improve efficiency and safety at its plants. One of the main focus areas is the means of transporting goods such as components, which require a lot of manpower and physical input. It has already tried and implemented other autonomous vehicles for component delivery indoors. However, the delivery between buildings, through outside routes, proved more difficult, because they can be affected by weather and be more complex, as obstacles and people are moving around, which can increase risk. MFTBC chose TractEasy to address these issues.
Sensors and cameras to map the surrounding environment
With a load capacity of 25 tons, the vehicle uses a range of sensors and cameras with real-time processing through its autonomous hauling. This includes centimeter-precise localization at any moment, wide-range perception to handle obstacles and enhanced navigation including vehicle to infrastructure (V2X) communication, predictive control, and decisions at intersections and pedestrian crossings. Powered by electricity, it also contributes to reducing CO2 emissions at production operations.