Hydrogen refueling, Daimler Truck and Linde launch new standard
The new process uses a new innovative sLH2 pump to slightly increase the pressure of the liquid hydrogen. This method facilitates a very robust fueling process that also keeps energy losses during refueling to a minimum. The pilot refueling station has a capacity of 400 kg of liquid hydrogen per hour.
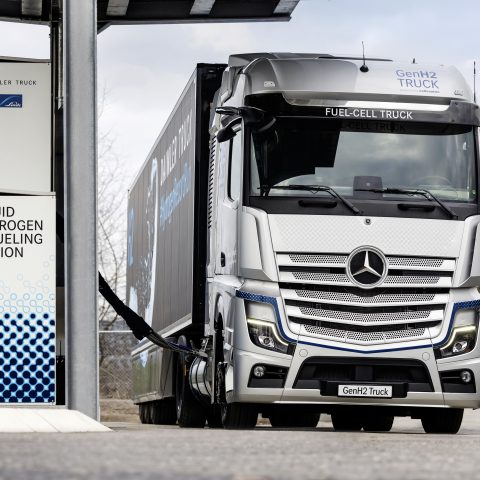
Daimler Truck and Linde launched sLH2, a jointly developed refueling technology for subcooled liquid hydrogen. When compared to gaseous hydrogen, this innovative approach allows for a higher storage density, a greater range, faster refueling, lower costs and superior energy efficiency.
Refueling takes around ten to fifteen minutes for a 40-ton heavy-duty truck, carrying 80 kg of liquid hydrogen for a range of 1,000 kilometers and more. At the same time, the new sLH2 technology lowers the required investment for a hydrogen refueling station by a factor of two to three, and operational costs are five to six times lower. Today, liquid hydrogen can be supplied reliably throughout Europe.
Daimler Truck and Linde to use innovative hydrogen refueling method
The new process uses a new innovative sLH2 pump to slightly increase the pressure of the liquid hydrogen. This method facilitates a very robust fueling process that also keeps energy losses during refueling to a minimum. Furthermore, no data transmission between the refueling station and vehicle is necessary, which further reduces the complexity of the solution.
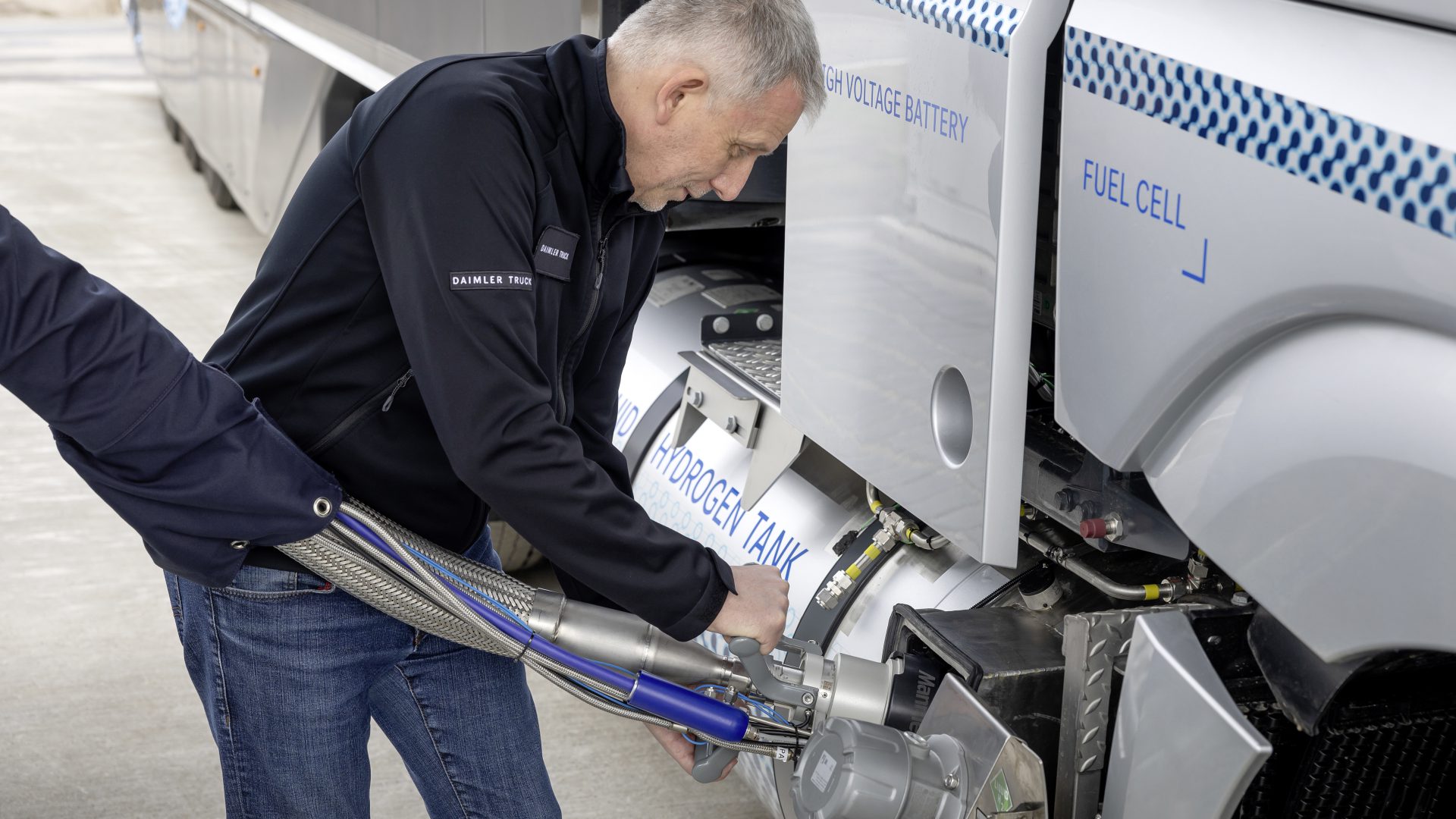
The pilot refueling station has a capacity of 400 kg of liquid hydrogen per hour. In comparison to regular liquid or gaseous hydrogen refueling concepts, sLH2 is considerably simpler while delivering increased performance. The new public sLH2 refueling station in Wörth am Rhein, Germany, sets a benchmark in terms of energy efficiency and performance. With energy consumption of only 0.05 KWh/kg, it requires approximately 30 times less energy compared with conventional gaseous hydrogen refueling.
To sum up, in contrast to current liquid hydrogen (LH2) refueling, the sLH2 process is similar to the convenience of current diesel refueling technology. Due to robust insulation the refueling hose and the design of the interfaces between the nozzle and fuel tank, the process is safe without the possibility of spillage. Therefore, the protective measures required for sLH2 refueling are comparable to those required for diesel. During the refueling process, cryogenic liquid hydrogen at minus 253 degrees Celsius can be filled into two connected 40 kg tanks mounted on either side of the truck chassis without the need for special safety gear. The sLH2 technology allows for high flow delivery of more than 400 kg of hydrogen per hour.
Statements from the partners
“Zero-emission transport needs three factors: the right battery-electric and hydrogen-powered vehicles, the required infrastructure network and cost parity for ZEVs compared to diesel trucks. In terms of vehicles, the transformation is in full swing. In terms of hydrogen infrastructure, we are reaching a major milestone today: With sLH2, hydrogen refueling becomes as convenient as today’s refueling with diesel. It takes about 10 to 15 minutes to fuel our Mercedes-Benz GenH2 Truck for a range of more than 1,000 kilometers. We now call on other OEMs and infrastructure companies to follow our approach and jointly make this technology an industry standard”, said Andreas Gorbach, Member of the Board of Management of Daimler Truck AG, responsible for Truck Technology.
“Subcooled liquid hydrogen considerably increases the efficiency of hydrogen refueling systems. The required investment is reduced by a factor of two to three, and operational costs are five to six times lower. This and further advantages make sLH2 a practical, CO2-neutral alternative to diesel in the heavy-duty vehicle sector. The technology we have developed with Daimler Truck will help pave the way for the development of a robust refueling network, which is essential to keep vehicles moving and supply chains intact”, added Juergen Nowicki, Executive Vice President Linde plc and CEO of Linde Engineering.