Regenerative braking, Tevva and ZF jointly develop high-efficiency system
The result is a system that recuperates up to four times more energy than a conventional compressed air brake system, optimising the range of the Tevva truck. Testing of the adapted system took place at the ZF test track in Jeversen, Germany.
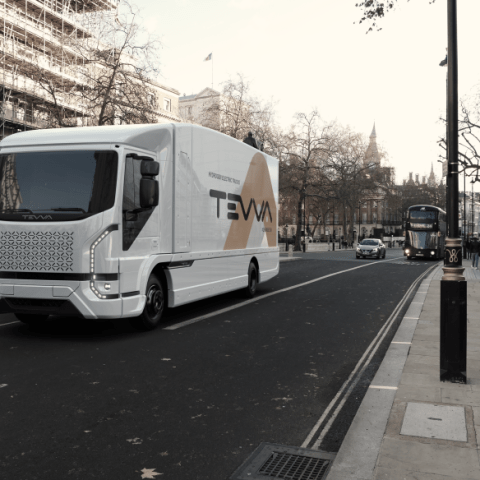
British e-truck manufacturer Tevva and German hi-tech component specialist ZF have jointly developed regenerative braking system for electric vehicles. Indeed, ZF electronic braking system (EBS) was adapted by Tevva engineers to be used in the Tevva 7.5 ton battery electric trucks. The latter use a blend of regenerative and compressed air brakes to add an extra layer of safety and responsiveness for drivers.
Tevva’s engineers successfully met a range of stringent testing criteria for the company’s truck to receive ZF’s approval, working on fine-tuning the electric truck’s vehicle control unit (VCU) and enhance compatibility with the EBS. The result is a system that recuperates up to four times more energy than a conventional compressed air brake system, optimising the range of the Tevva truck. Testing of the adapted system, which took place at the ZF test track in Jeversen, Germany, involved a variety of conditions, gradients and surface types.
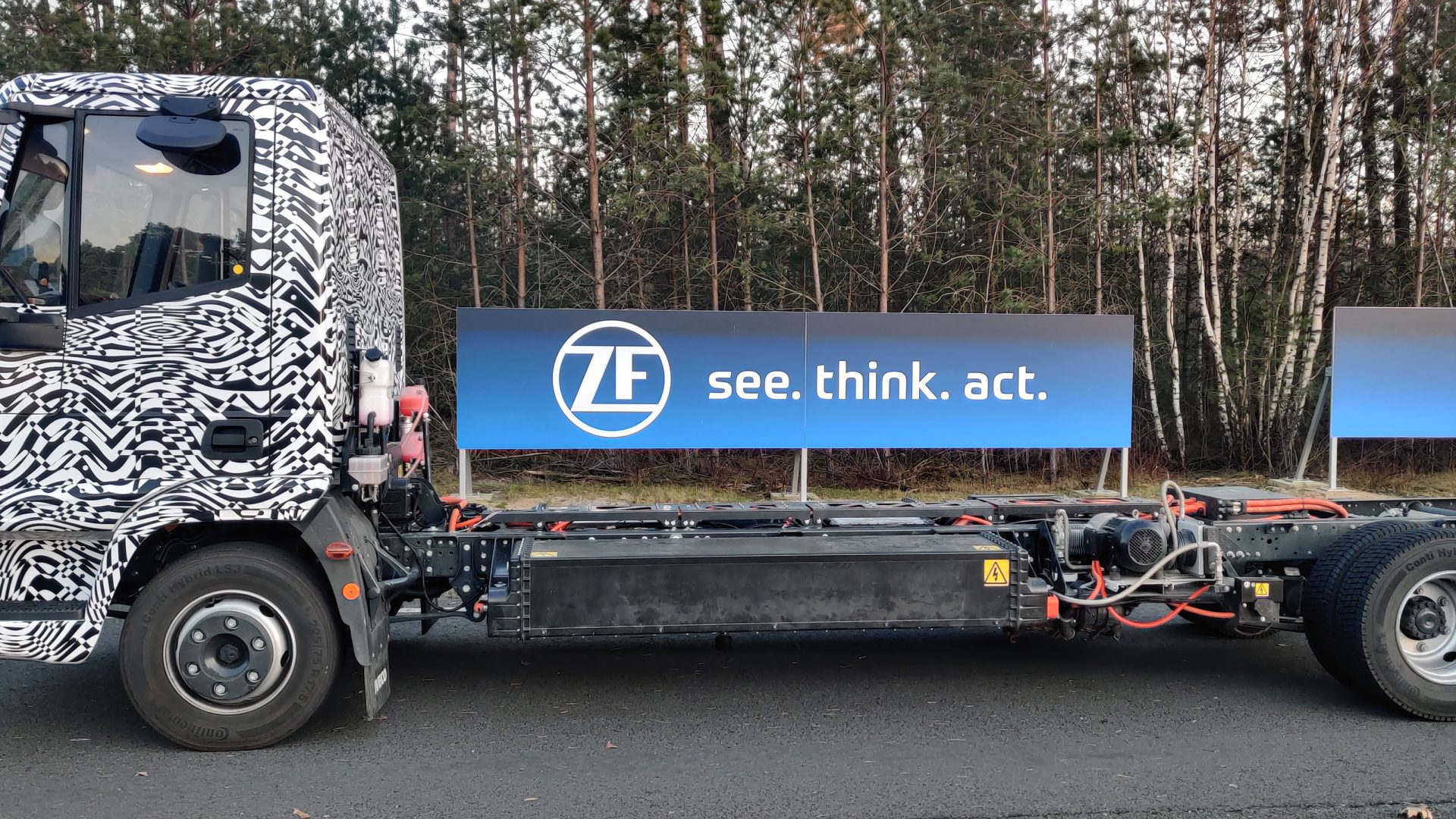
Regenerative braking, more into technical details
Technological advancements allow a modern EBS system to control the blending of friction braking with the e-motor, reducing brake wear and tear. The system transfers the driver’s deceleration request electronically to all braking system components to shorten response time, balance brake forces and provide ease of braking and efficient brake management.
ZF’s Heiko Eggers, Head of Commercial Vehicle EMEA Application Engineering for Braking and ADAS, said: “Our broad product portfolio, including ZF’s standardised Electronic Braking System, enables faster time-to-market for new, innovative market players such as Tevva. Their commitment and agile engineering expertise allowed us to meet our stringent safety requirements and complete our project. We look forward to seeing the first Tevva trucks on the road”.
Tevva’s Uzair Jilani, Lead Engineer, Drive and Brake Systems, added: “We have worked hard to secure a ringing endorsement from arguably one of the world’s most significant Tier 1 suppliers. Working with ZF is a crucial step in the momentum we are building as a truck manufacturer. The system has been adapted for use with our regen system; when the brake pedal is pushed, most of the ‘braking’ is handled by regen, meaning that the drive system slows the vehicle down”.