TotalEnergies and Valeo to jointly develop EV battery cooling systems
The two partners are thinking of an innovative way of cooling EV batteries by using a new dielectric fluid. TotalEnergies has developed a dielectric coolant that can be in direct contact with battery cells. Valeo will contribute its expertise in the related thermal systems to design and build the best solution to integrate the coolant within the electric vehicle battery pack.
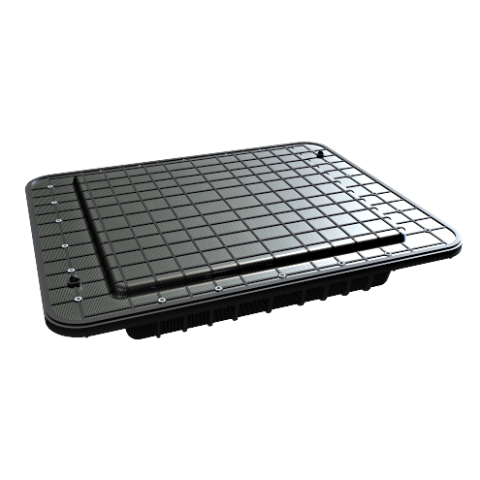
TotalEnergies and Valeo, two primary French groups, decided to cooperate in order to jointly develop battery cooling systems addressed to electric vehicles. The two partners are thinking of quite an innovative way of cooling electric vehicle batteries by using a new, very high-performance dielectric fluid that makes it possibile to reduce carbon footprint.
As the companies explain, with current technology, fluids cannot be used to cool the battery from within. TotalEnergies has developed an innovative dielectric coolant that can be in direct contact with battery cells. Valeo will contribute its expertise in the related thermal systems to design and build the best solution to integrate the coolant within the electric vehicle battery pack, thereby optimizing performance by conditioning it at the right temperature.
Potrebbe interessarti
Increasing safety on level 4 autonomous vehicles, Navya and Valeo form all-French partnership
TotalEnergies and Valeo share R&D efforts
Research conducted under the agreement will enable Valeo to reduce the weight of the thermal systems used to cool vehicle batteries – greatly improving the overall weight, travel range and carbon footprint of electric vehicles – and improve safety in response to battery fire risk.
“The dielectric fluid developed by TotalEnergies rounds out our TotalEnergies QUARTZ EV Fluid range aimed at electric mobility. It is a unique and innovative solution that aims to contribute to the decarbonization of the electric mobility sector – one of the company’s strategic priorities”, stated Philippe Charleux, Senior Vice President, Lubricants & Specialties at TotalEnergies.
“Helping to reduce the impact of mobility is central to Valeo’s strategy”, added Francisco Moreno, President of Valeo’s Powertrain Systems Business Group. “Technologies that contribute to reducing CO2 emissions now account for 60% of Group sales, and Valeo plans to continue expanding its portfolio of solutions that promote low-carbon mobility”.